1. Проблема: разбрызгивание шлака.
В процессе лазерной сварки расплавленный материал разбрызгивается повсюду и прилипает к поверхности материала, в результате чего на поверхности появляются металлические частицы, влияющие на красоту изделия.
Причина проблемы: разбрызгивание может быть связано с чрезмерной мощностью, приводящей к слишком быстрому плавлению, а также с загрязнением поверхности материала или слишком сильным газом.
Решение: 1, соответствующая регулировка мощности; 2. Обратите внимание на очистку поверхности материала; 3. Уменьшите давление газа.
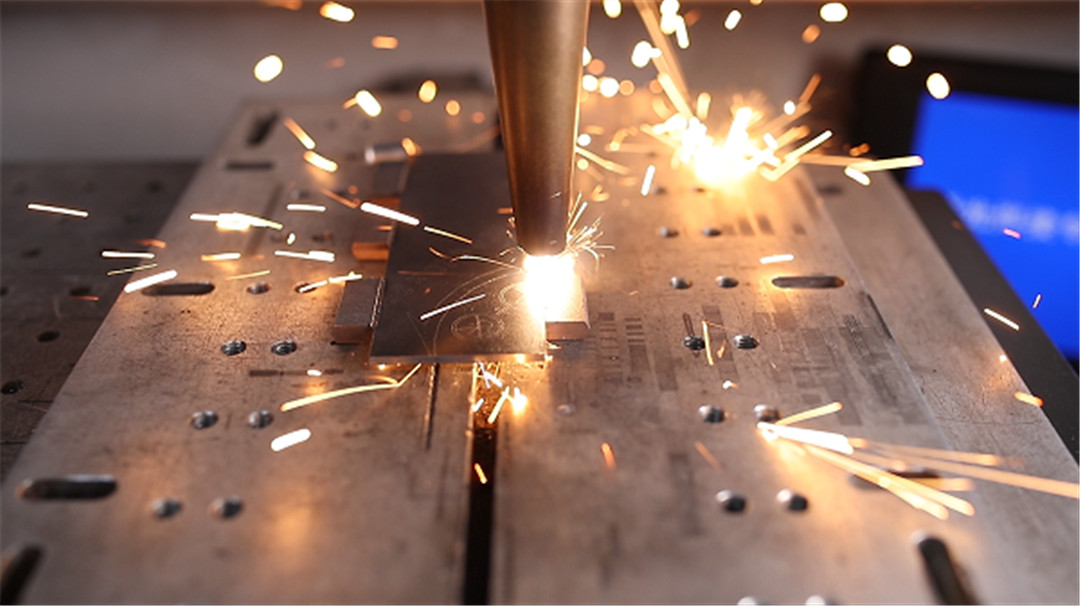
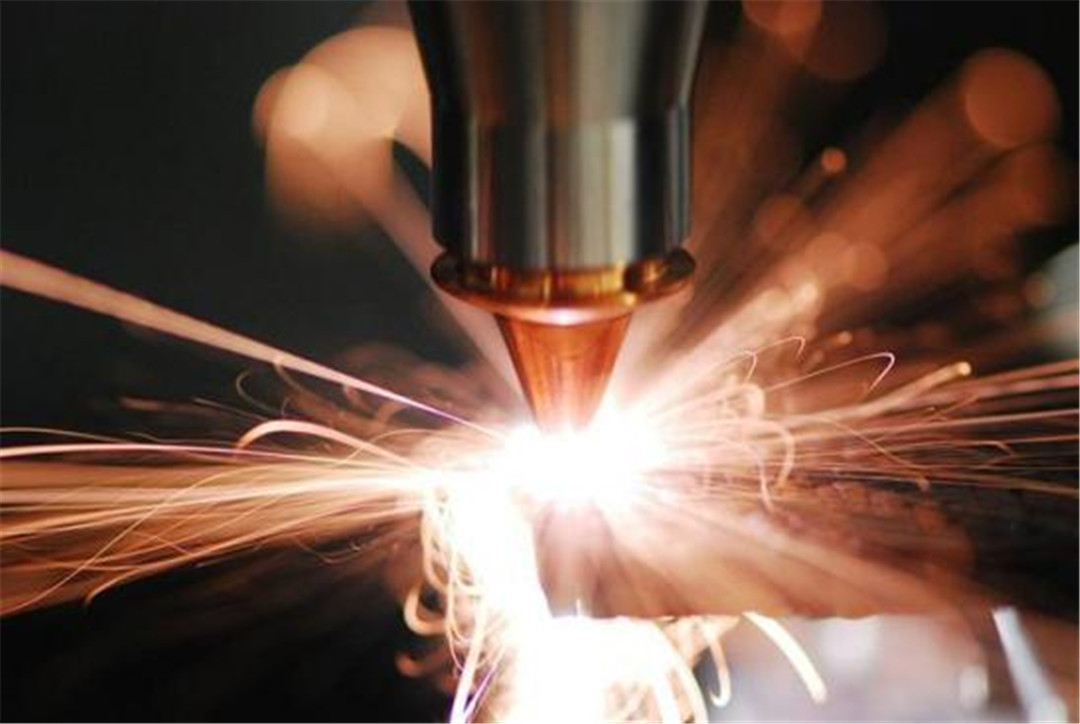
2. Проблема: сварной шов расположен слишком высоко.
Сварщик обнаружит, что сварочный шов значительно выше обычного уровня, в результате чего сварной шов получается толстым, что выглядит очень непривлекательно.
Причина проблемы: слишком высокая скорость подачи проволоки или слишком низкая скорость сварки.
Решение: 1. Уменьшить скорость подачи проволоки в системе управления; 2. Увеличьте скорость сварки.
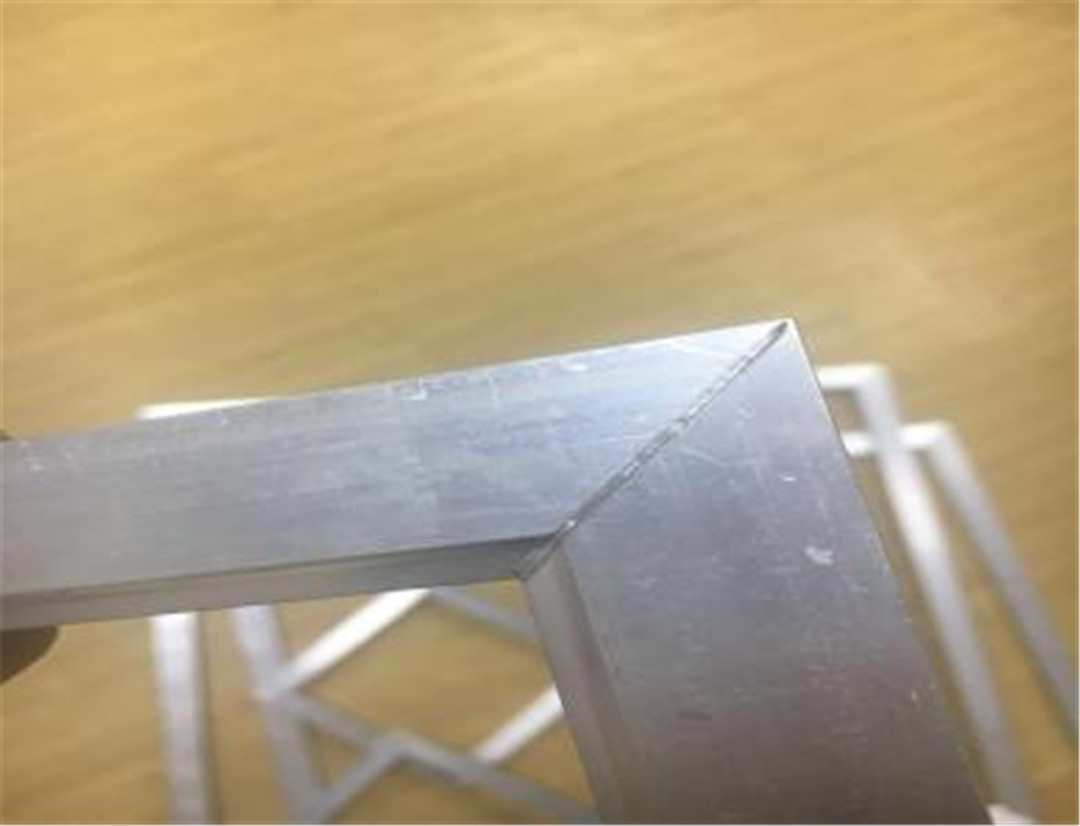
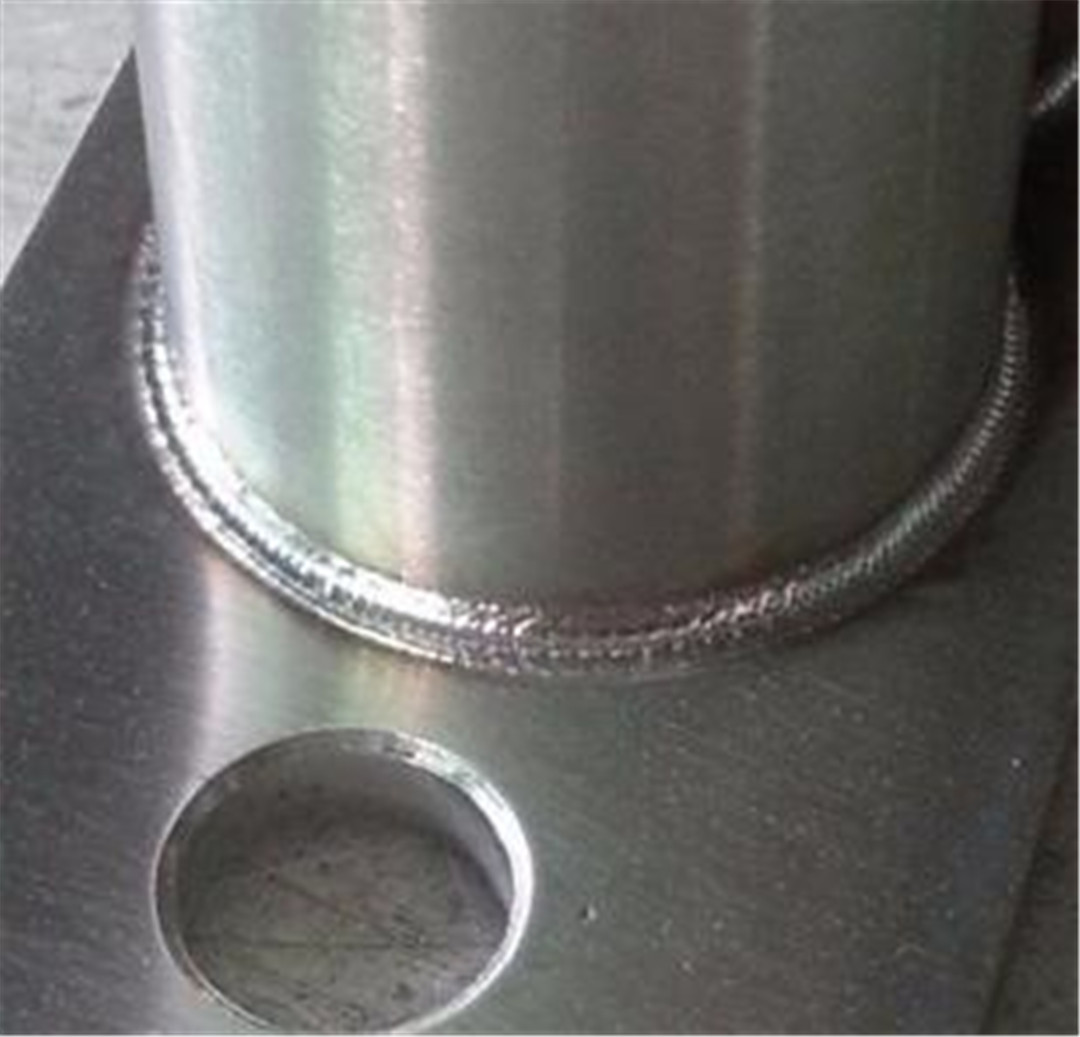
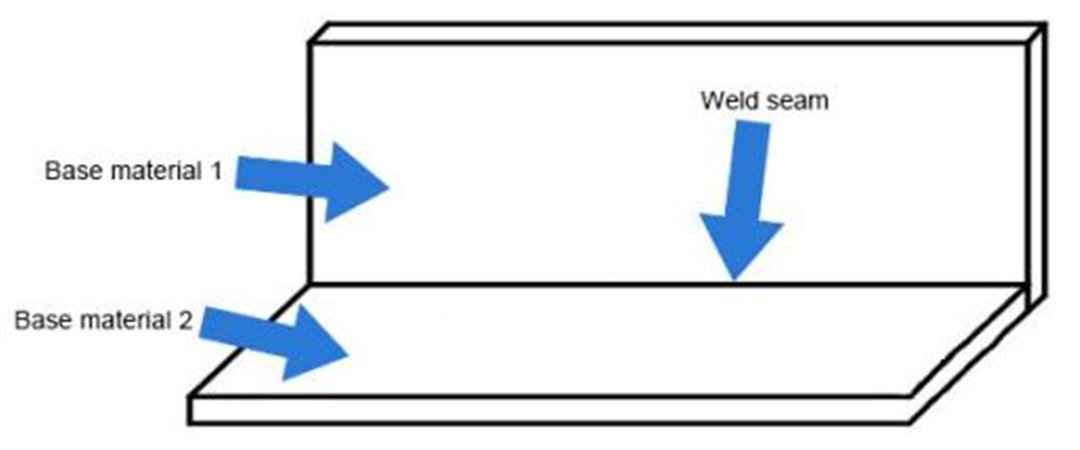
3. Проблема: смещение сварного шва.
Сварка без затвердевания на стыках конструкций и неточная их установка могут привести к полному отказу сварки.
Причина проблемы: неточное позиционирование при сварке; несогласованное положение подачи проволоки и лазерного облучения.
Решение: 1. Отрегулируйте смещение лазера и угол поворота на доске; 2. Проверьте соединение между механизмом подачи проволоки и лазерной головкой на предмет отклонений.
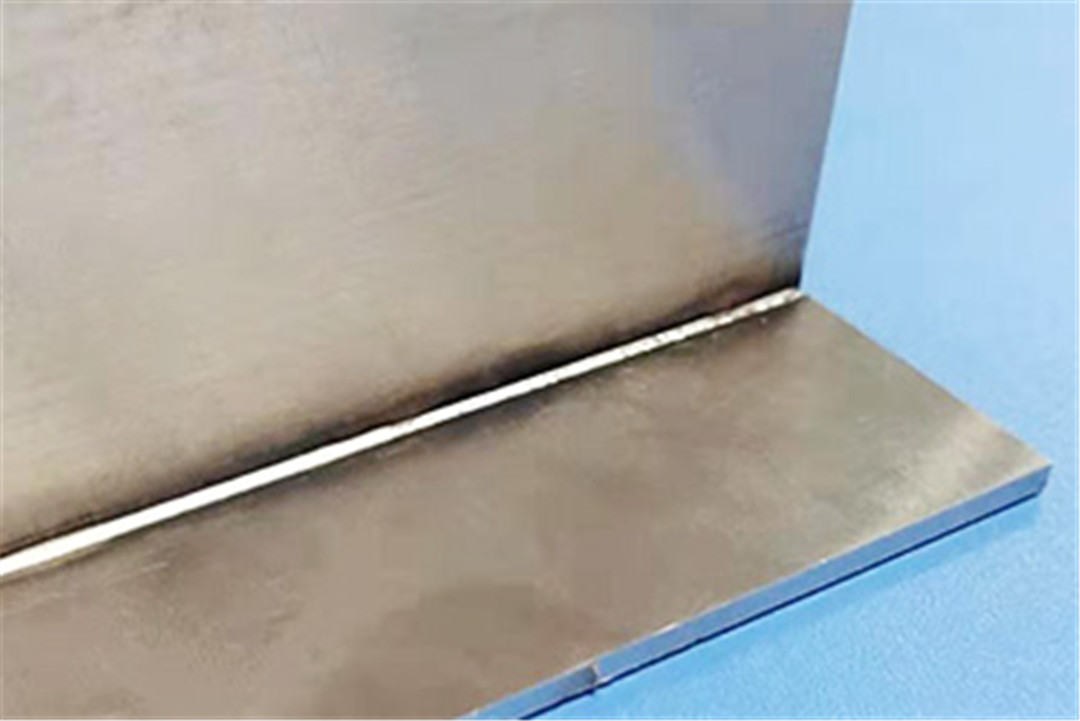
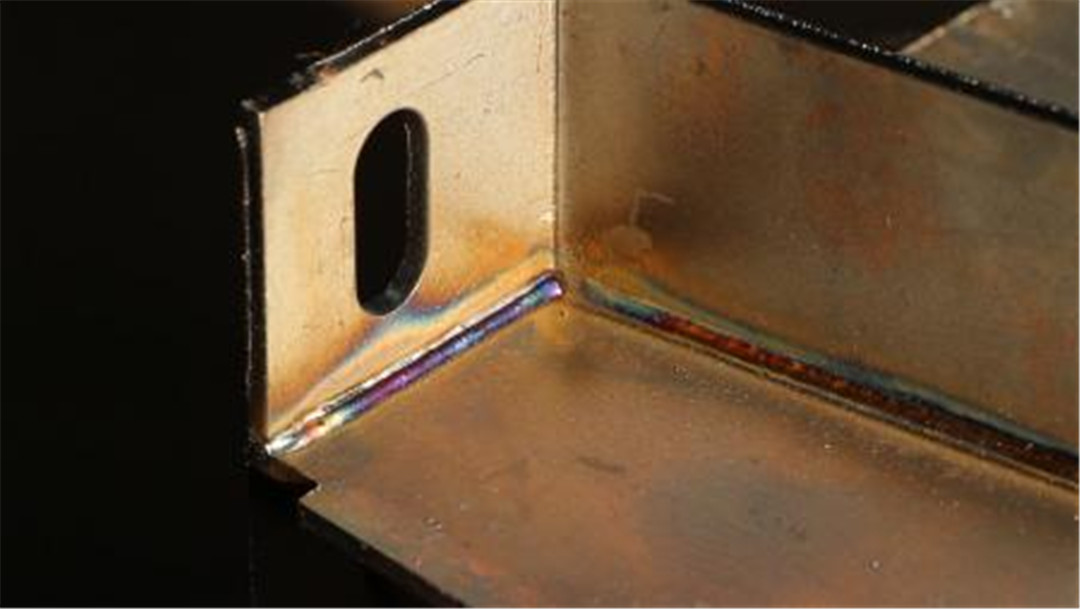
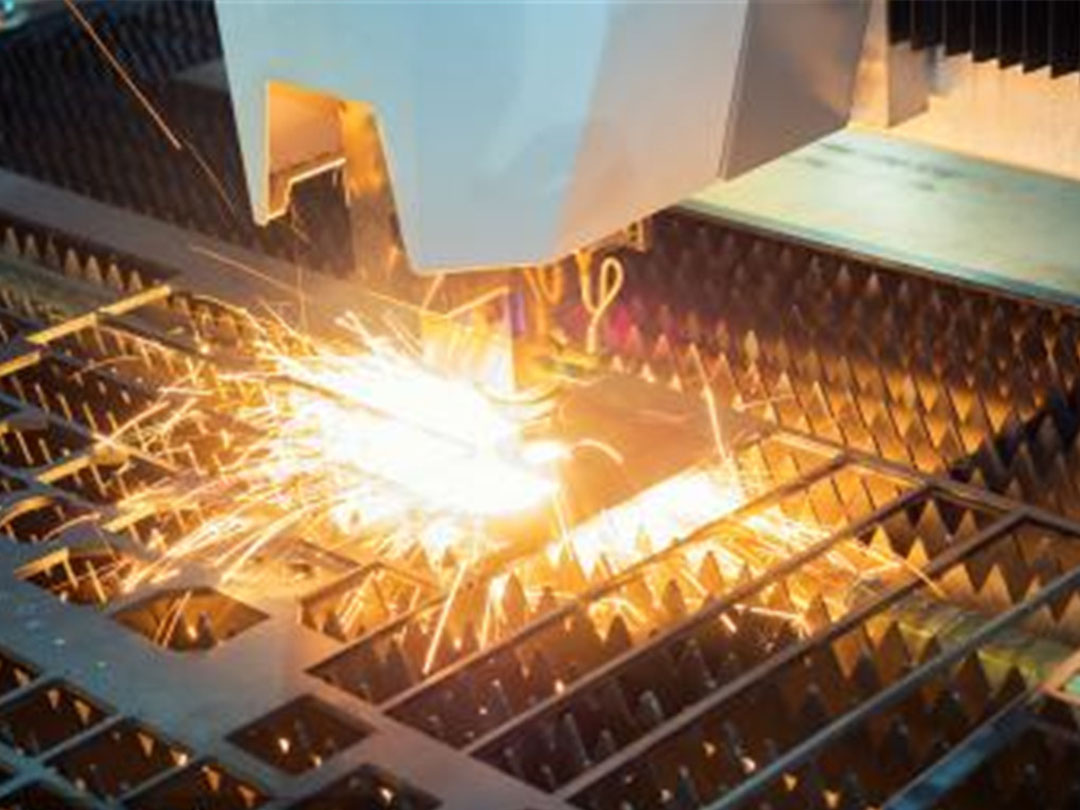
4. Проблема: цвет сварного шва слишком темный.
При сварке нержавеющей стали, алюминиевого сплава и других материалов цвет сварного шва слишком темный, что приводит к сильному контрасту сварного шва и поверхности материала, что чрезвычайно влияет на красоту.
Причина проблемы: мощность лазера слишком мала, что приводит к недостаточному сгоранию, или слишком высокая скорость сварки.
Решение: 1. отрегулируйте мощность лазера; 2. отрегулируйте скорость сварки.
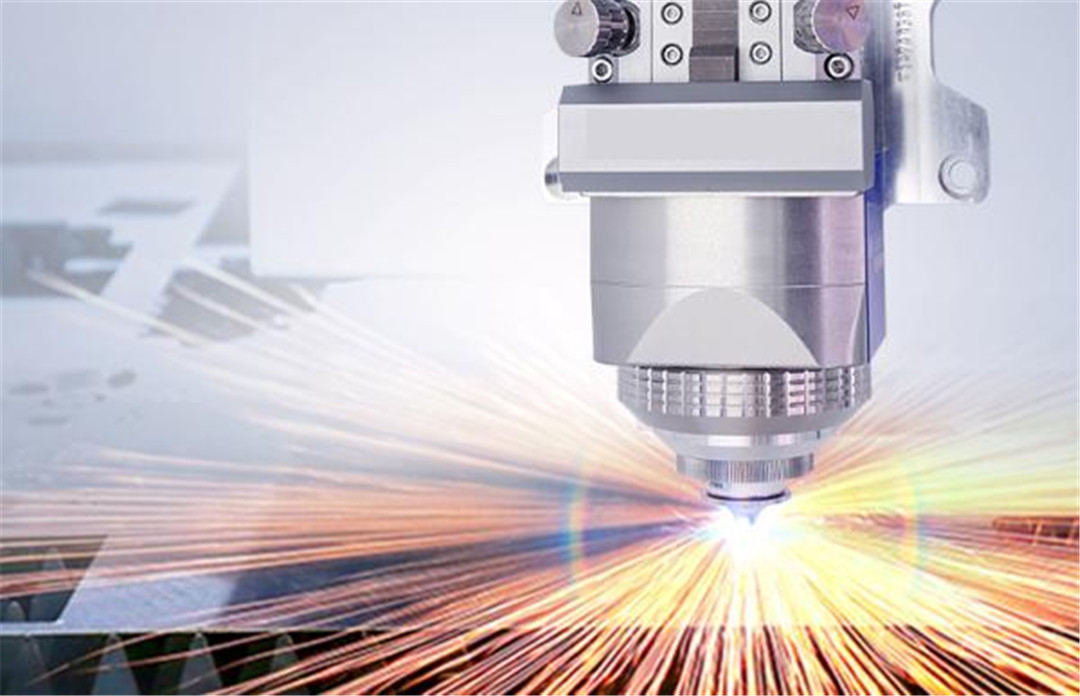
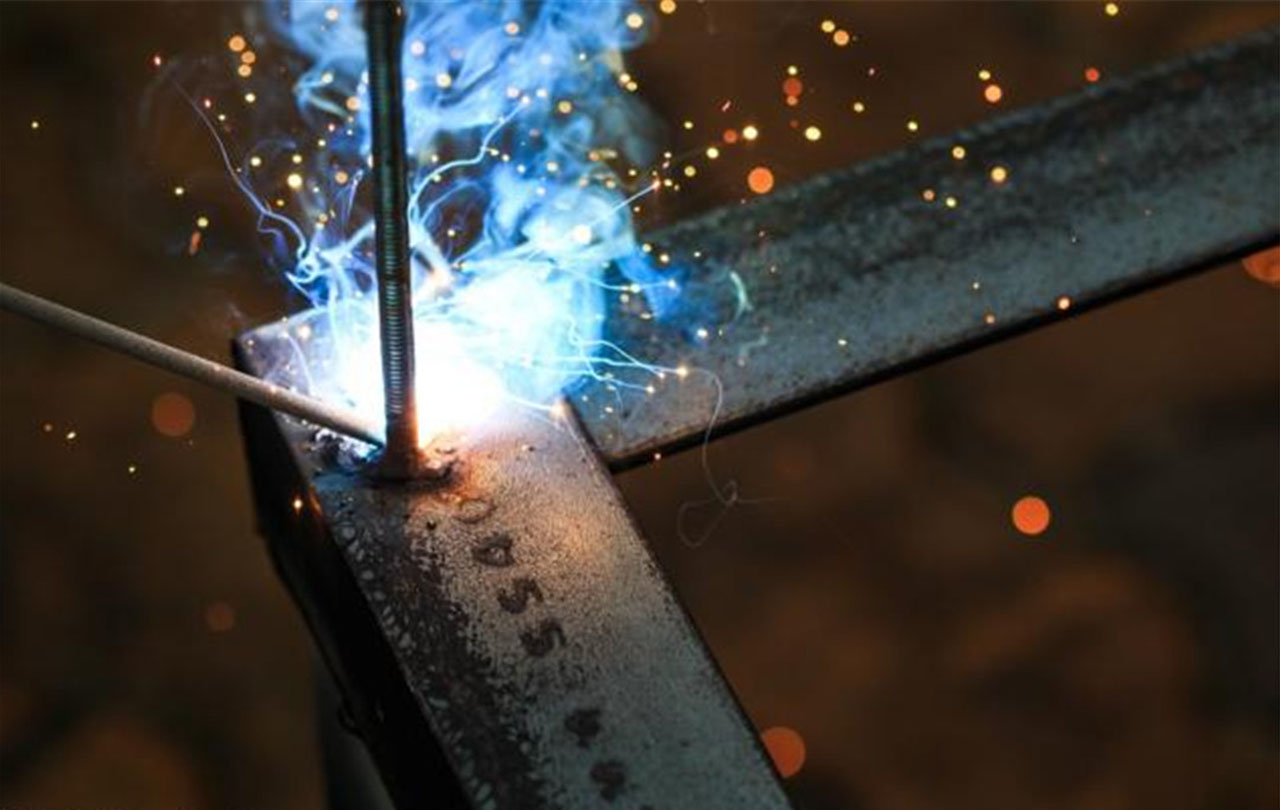
5. Проблема: неровная угловая сварка молдинга.
При сварке внутренних и внешних углов углы не регулируются по скорости или положению, что может легко привести к неравномерности сварки в углах, что влияет как на прочность сварного шва, так и на его внешний вид.
Причина проблемы: неудобное положение при сварке.
Решение: Отрегулируйте смещение фокуса в системе управления лазером так, чтобы ручная лазерная головка могла выполнять сварочные операции вбок.
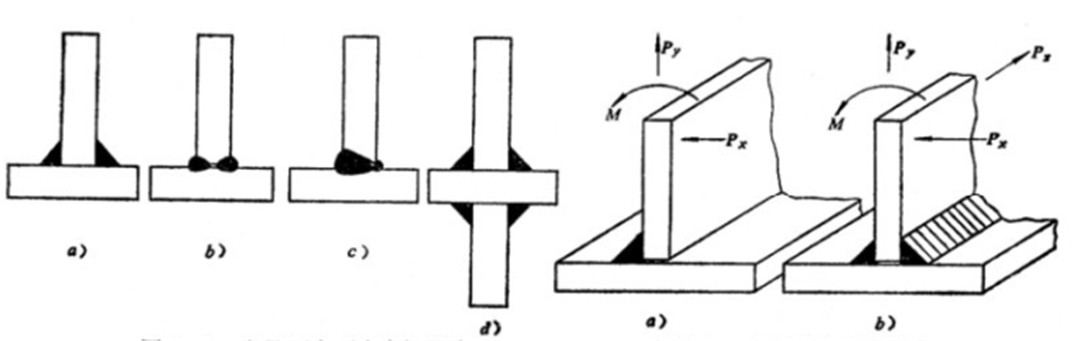
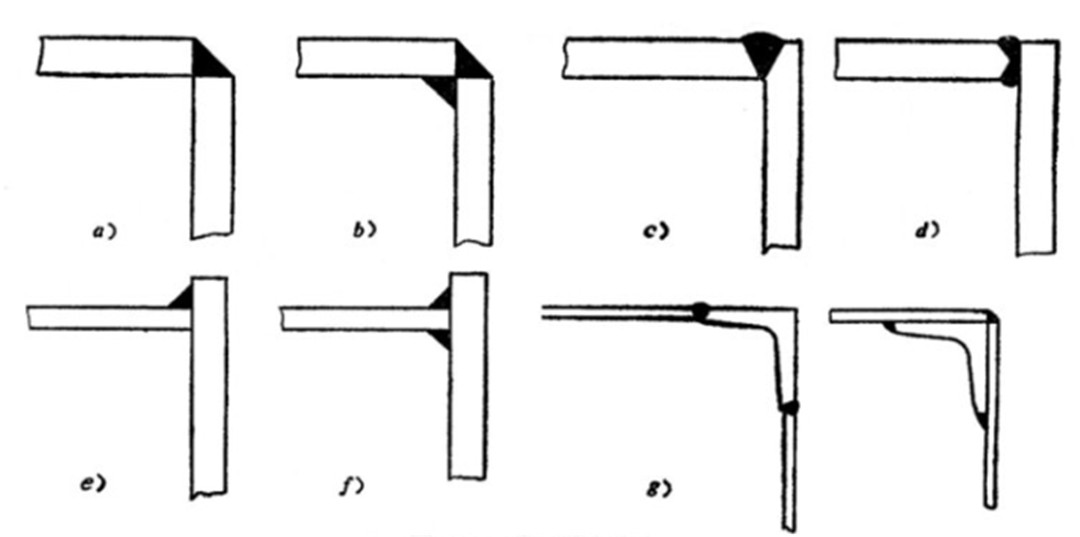
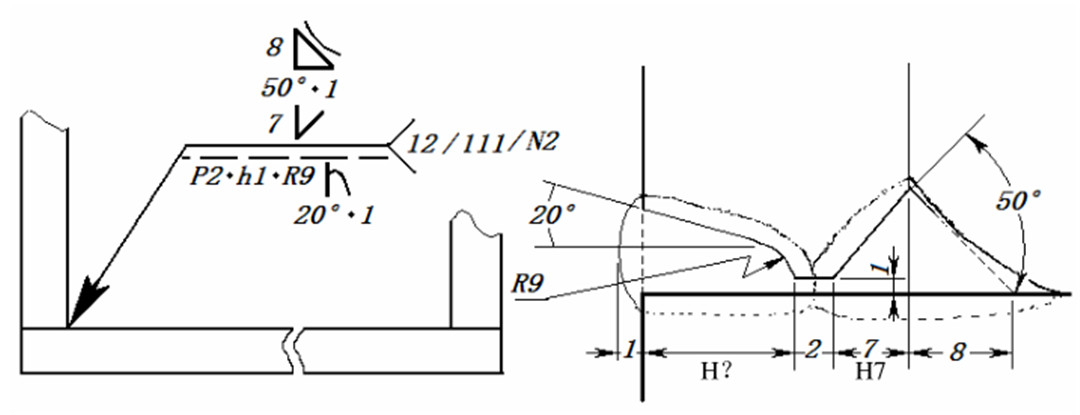
6. Проблема: депрессия сварочного шва.
Вмятины в сварном соединении приведут к недостаточной прочности сварки и некачественной продукции.
Причина проблемы: слишком большая мощность лазера или неправильно настроен фокус лазера, в результате чего ванна расплава становится слишком глубокой и материал переплавляется, что, в свою очередь, приводит к вдавливанию сварного шва.
Решение: 1. Отрегулируйте мощность лазера; 2. Отрегулируйте фокус лазера.
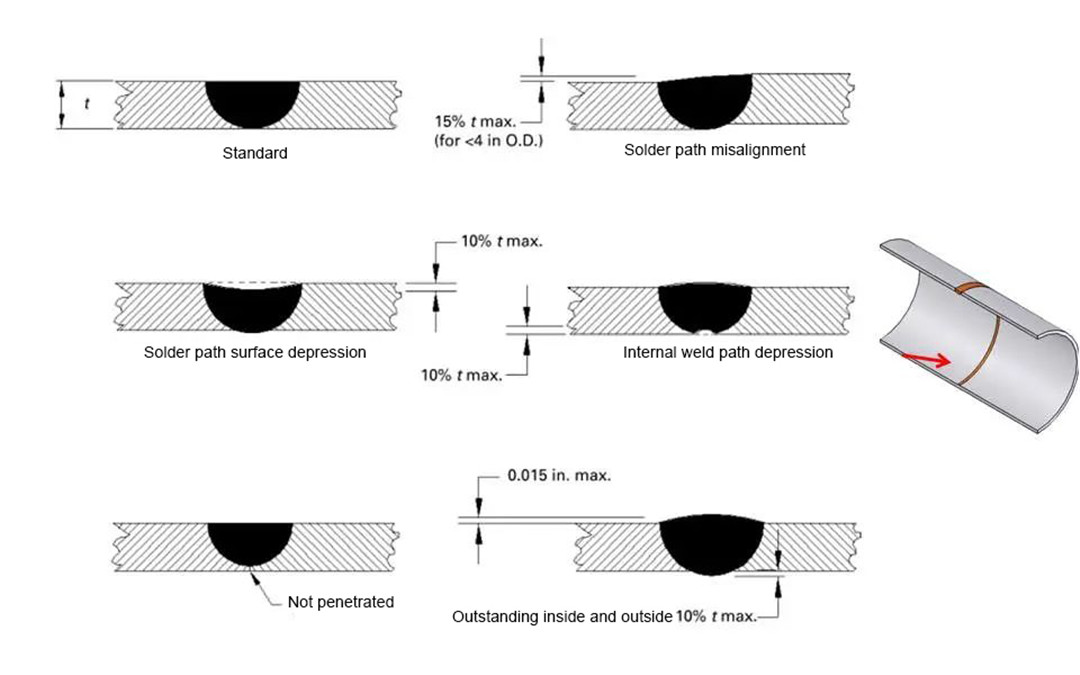
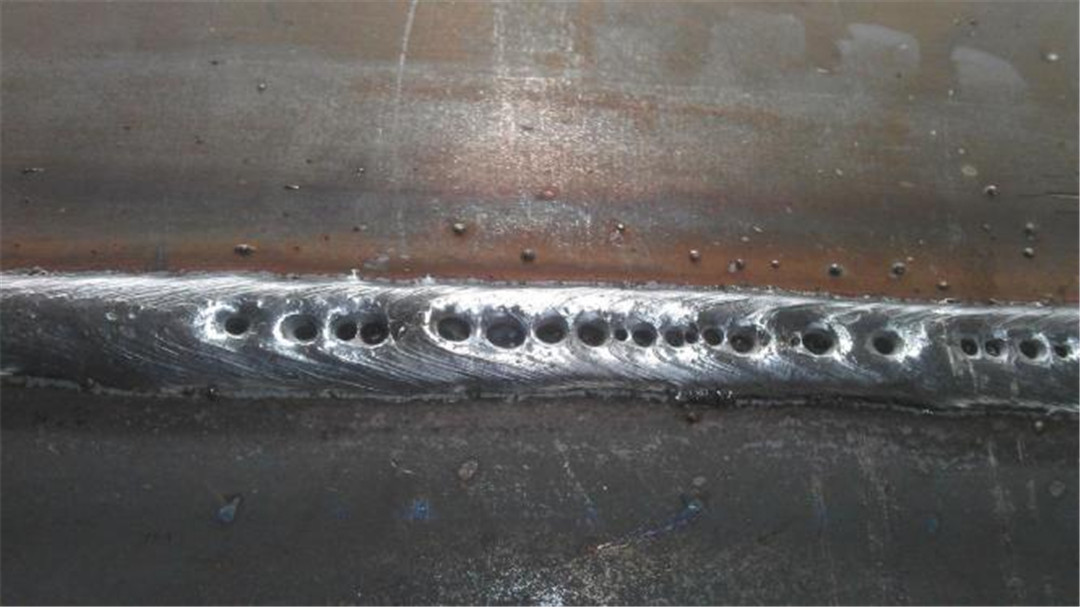
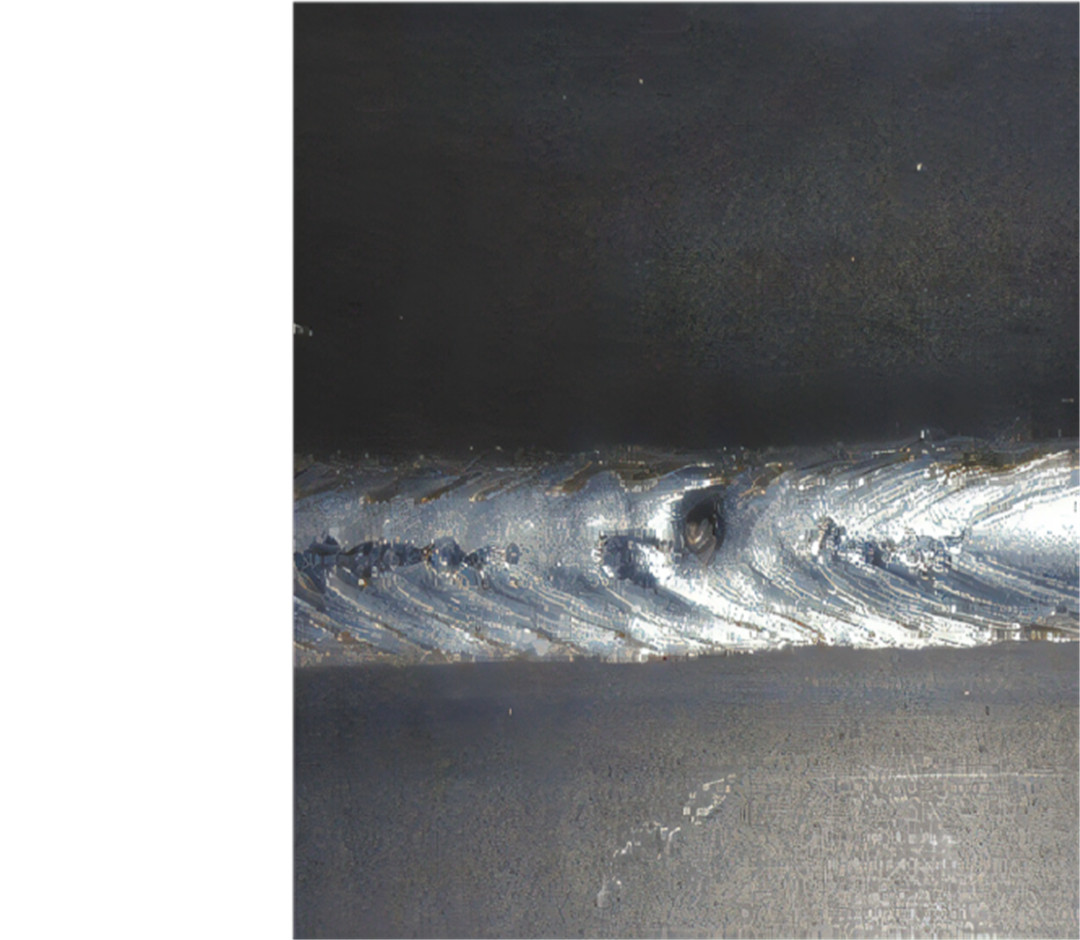
7. Проблема: толщина сварного шва неоднородна.
Сварной шов иногда слишком большой, иногда слишком маленький, а иногда нормальный.
Причина проблемы: освещение или подача проволоки не являются проблемой.
Решение: Проверьте стабильность лазера и механизма подачи проволоки, включая напряжение источника питания, систему охлаждения, систему управления, заземляющий провод и т. д.
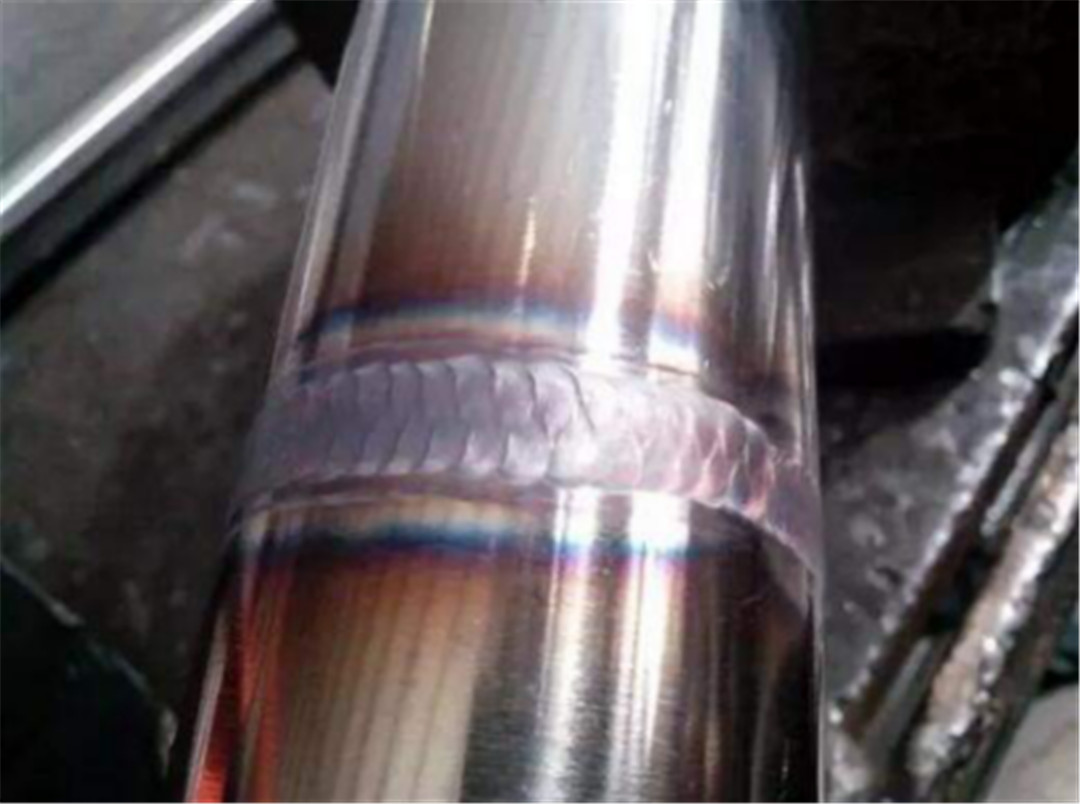
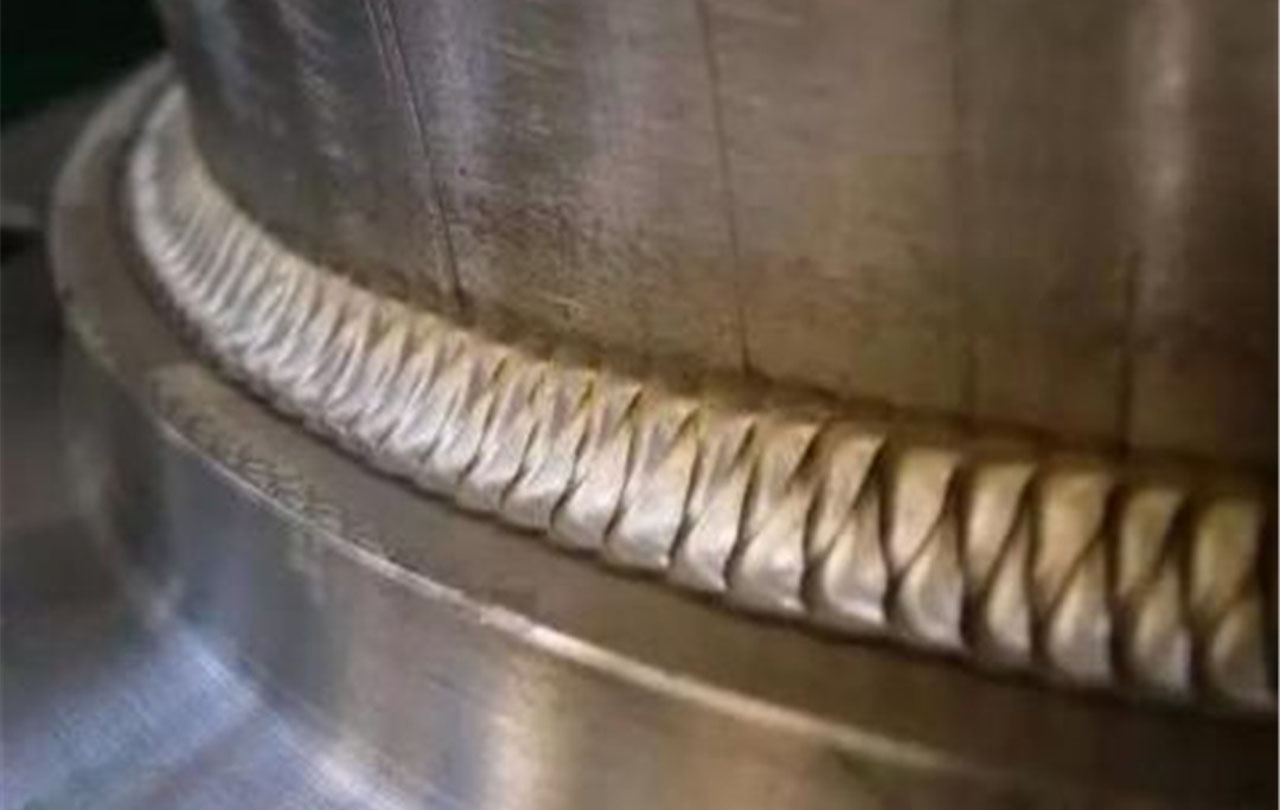
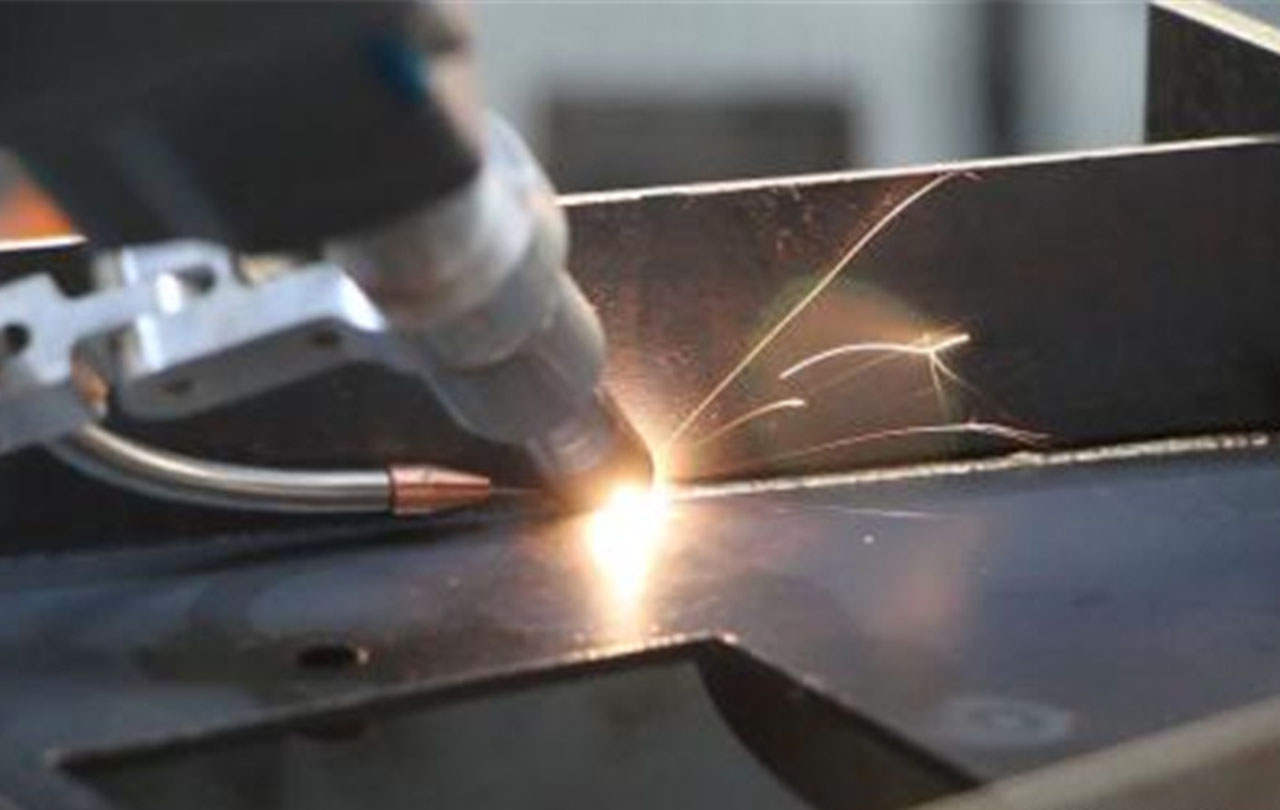
8. Проблема: острые углы
Прикусная кромка относится к сварному шву, а материал плохо сочетается, скашивается и другие условия, что влияет на качество сварки.
Причина проблемы: скорость сварки слишком высока, в результате чего ванна расплава распределяется неравномерно по обеим сторонам материала, или зазор между материалом велик, присадочного материала недостаточно.
Решение: 1. Отрегулируйте мощность и скорость лазера в зависимости от прочности материала и размера сварного шва; 2. Работы по заполнению или ремонту провести позже.
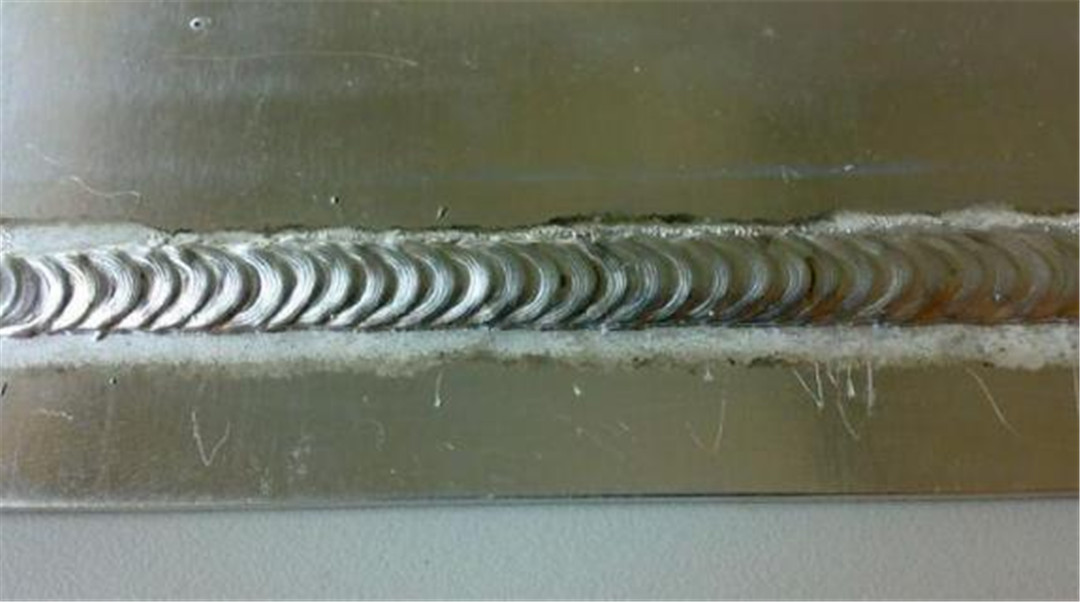
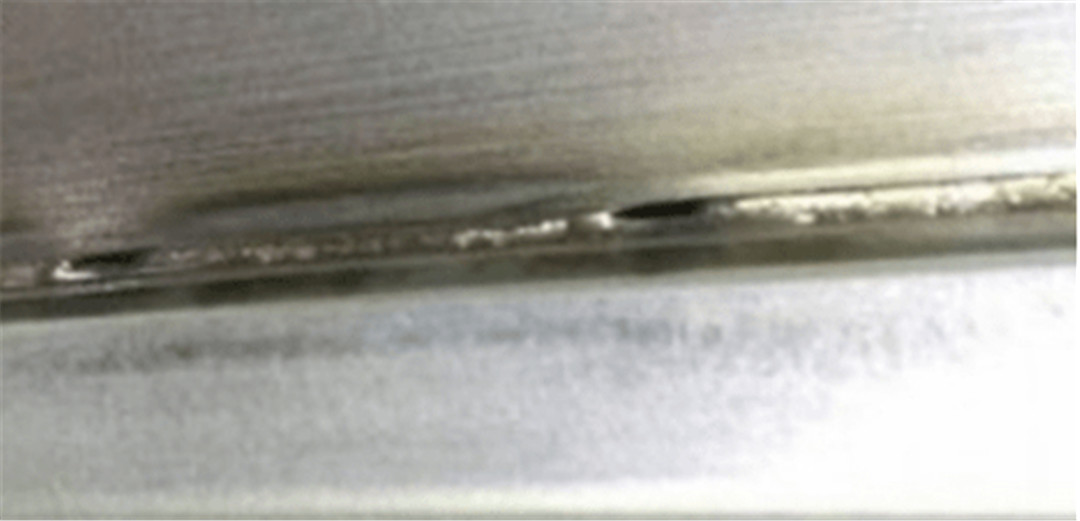
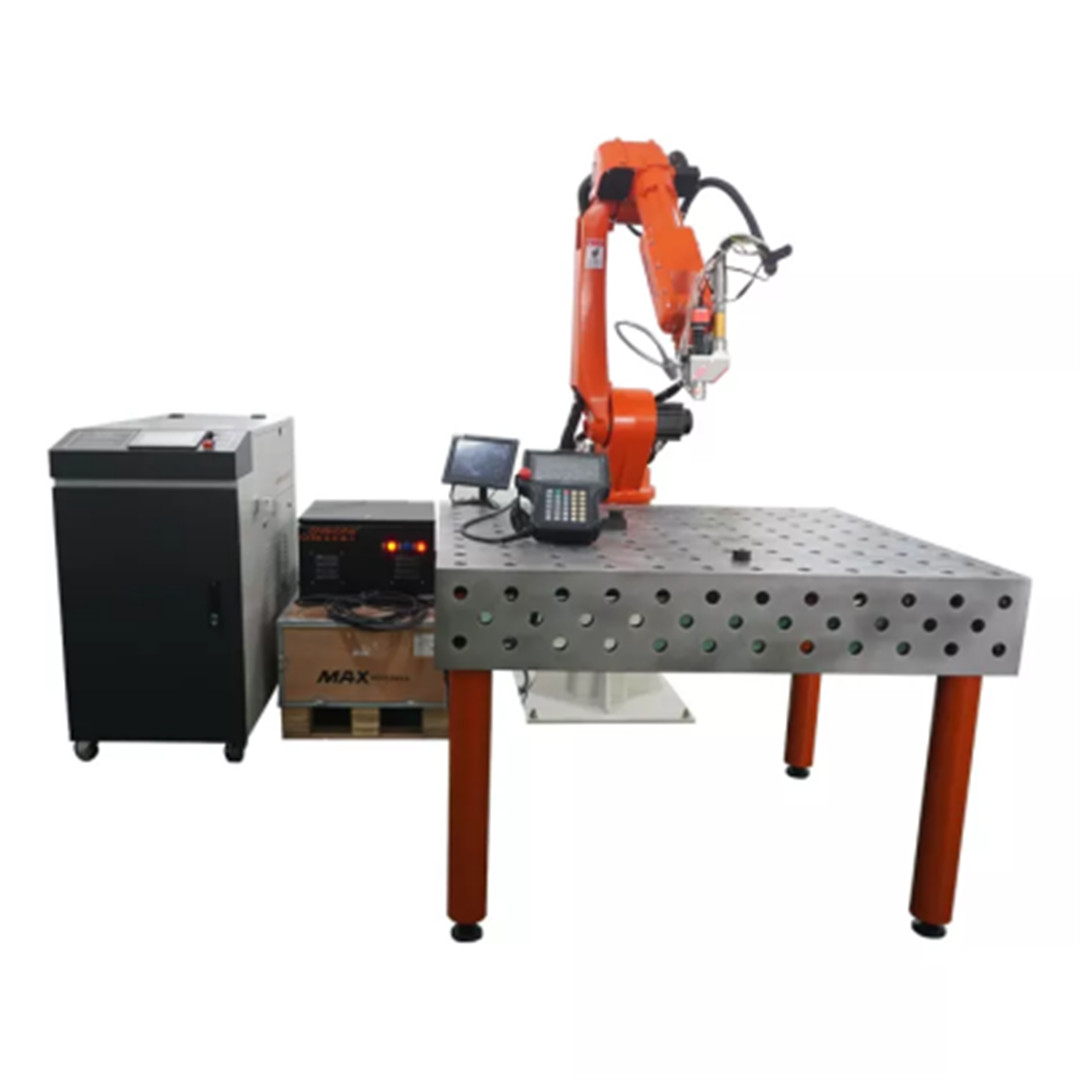
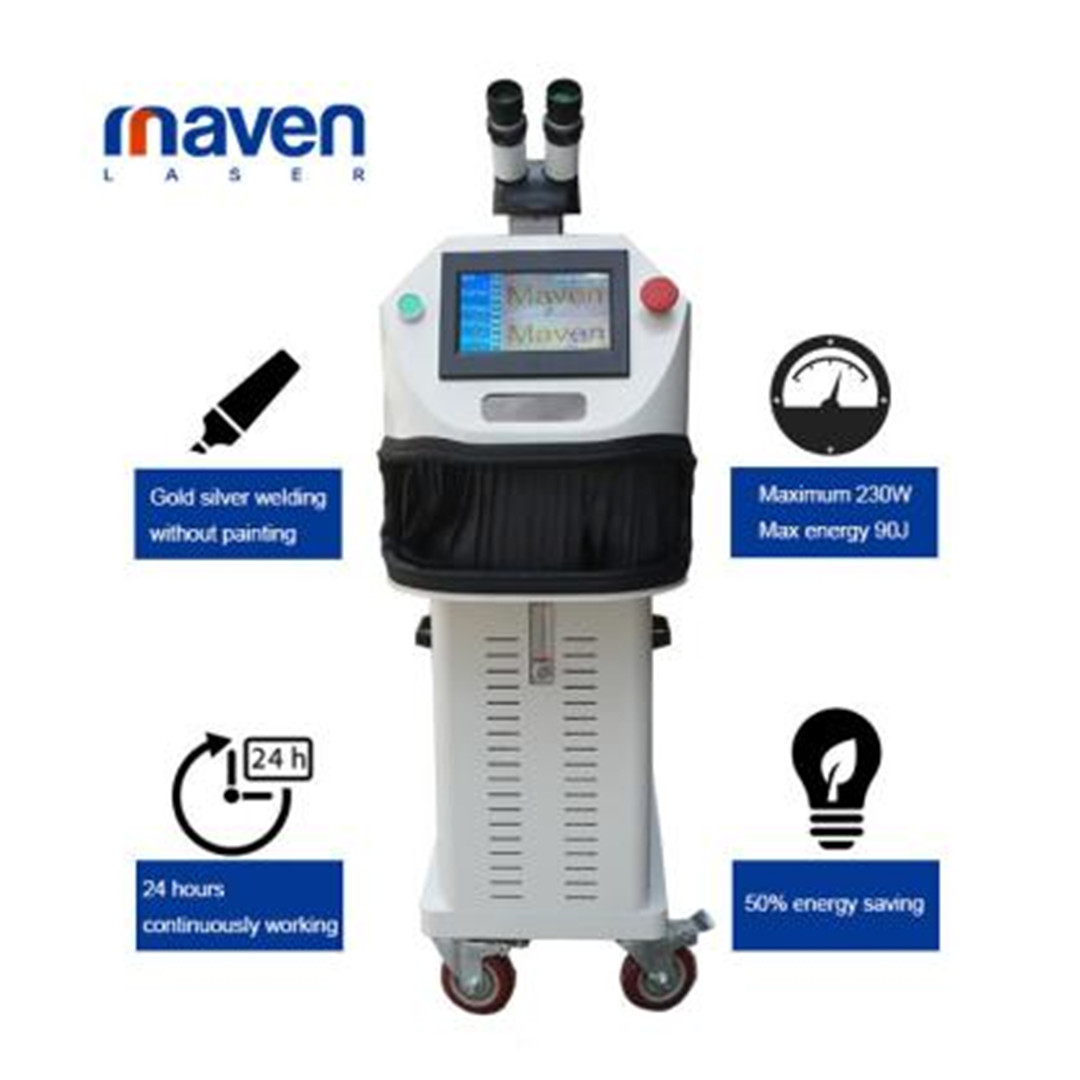
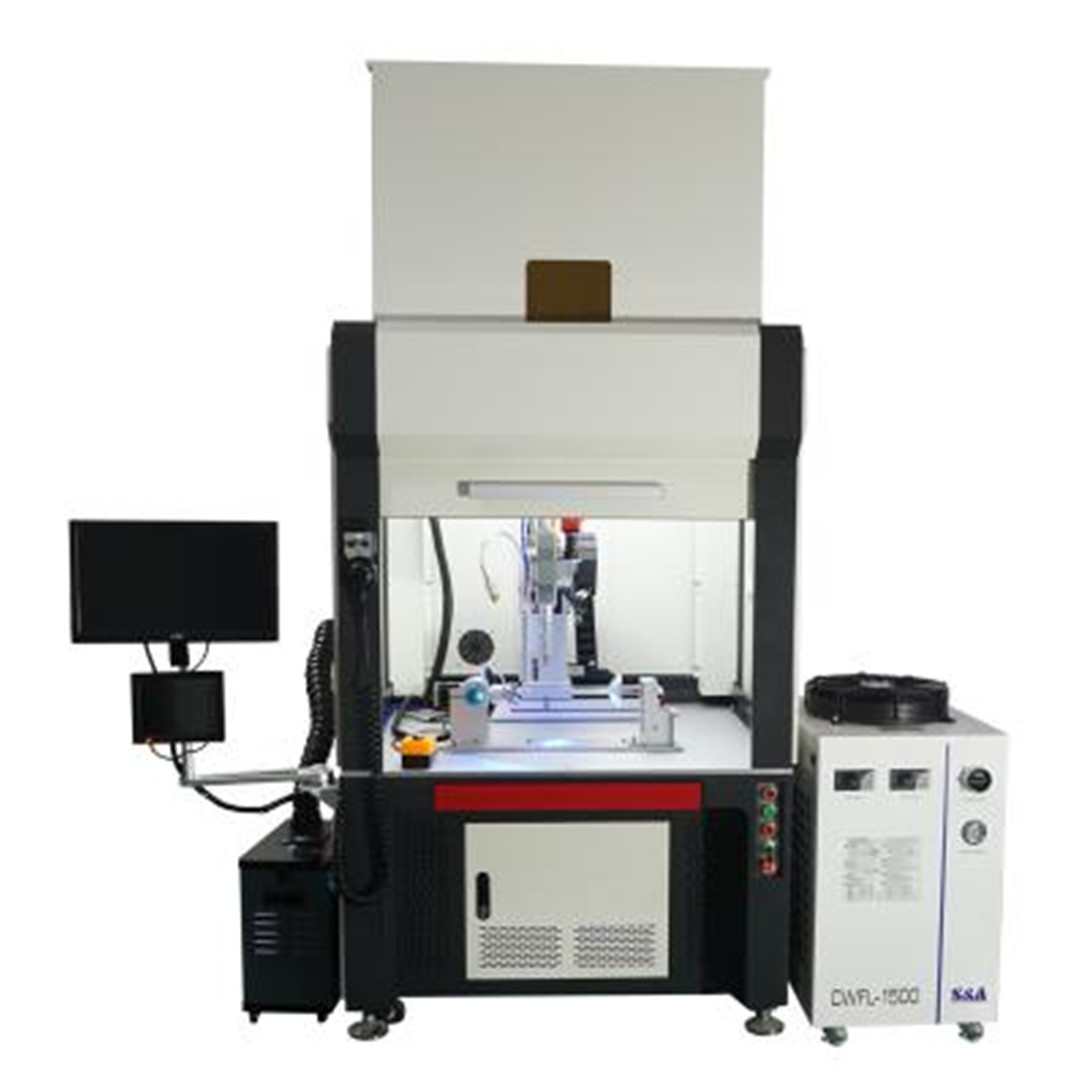
Maven Laser Automation Co., Ltd. (сокращенно Maven laser) — ведущий производитель лазерных систем и профессиональных решений для автоматизации, расположенный в Шэньчжэне, Китай, основанный в 2008 году. Наша профессиональная продукция: машины для лазерной очистки, машины для лазерной сварки, машины для роботизированной сварки и машины для сварки платформ, если У вас есть какие-либо профессиональные вопросы, добро пожаловать к нам.
Время публикации: 18 ноября 2022 г.